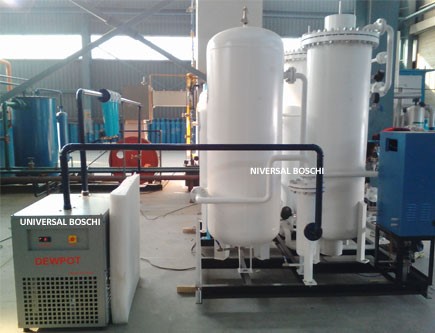
Nitrogen is an important gas that has extensive applications in various industries. It also finds usage in biotechnology and the medical field. Production of nitrogen for commercial purposes is undertaken with a nitrogen gas plant. We use cryogenic distillation technology in the making of the machinery. This is known as the most popular technology in the industry. It functions by liquefaction of atmospheric air for the separation of nitrogen from other gases. The plant is equipped to generate nitrogen with high purity in both liquids as well as gaseous form.
Nitrogen plants are fully automated and can be operated by a single semi-skilled operator. We also provide a vaporizer with a plant for converting liquid nitrogen into a gaseous form. Businesses prefer liquid nitrogen because it is easy to store and transport. It is less likely to leak so it is economical and would save you a lot of money over a period of time. Being the leader in manufacturing liquid nitrogen plant, we have earned the trust of customers from all over the globe for fabricating high-quality plant machinery. We use only the best materials and components in the industrial gas market.
Different processes for the generation of liquid nitrogen
Liquid nitrogen (LN2) production is accomplished mainly through three well-known techniques known as pressure swing adsorption, membrane adsorption, and cryogenic distillation. All three have their pros and cons. However, it depends upon the requirements & proclivity of the customers which process he thinks fits his LN2 production requirements. All three processes are described below:
Pressure swing adsorption (PSA) process
PSA is widely used for generating industrial gases like nitrogen and oxygen with high purity. This process uses two towers equipped with carbon molecular sieves (CMS) through which the atmospheric air is passed. The air enters from the bottom of the tower and then moves through the CMS, which is made up of zeolite and silica. Ambient air is compressed before it is introduced into the CMS for adsorption. On being passed through a high-pressure column, unwanted gases like oxygen and water vapors are adsorbed in the carbon molecular sieve while nitrogen is allowed to go through which is collected and stored. Unwanted oxygen and water vapors are evaporated back into the atmosphere.
PSA process requires the towers to be pressurized at a set period and then depressurized back to atmospheric pressure with low adsorbing gases leaving the column first followed by other gases. When adsorption takes place under vacuum conditions it is called vacuum swing adsorption (VSA). To reduce the system rundown time during the pressurizing and depressurizing process two or more adsorbents are used. PSA process of nitrogen production is considered an efficient method for lower daily production, up to 20-100 tons of nitrogen.
Membrane separation process
The most important part of the membrane process is called the separation membrane, which comprises thousands of hollow fibers. Just like the PSA process, the air is first compressed and then it is passed through the membrane. Hollow fibers are permeable to gas molecules with some gases passing through the membrane more easily than the others. Gases like oxygen, water vapors, and CO2 are fast gases that pass through the membrane easily and are evaporated back into the atmosphere. Nitrogen being a slow gas passes through the membrane rather slowly generating a high purity stream of nitrogen collected at the outlet of the membrane. Other equipment is important for controlling the flow rate, pressure, and purity. Manufacturing of membrane nitrogen generators is done with high-quality ASME certified materials for steady performance.
Cryogenic distillation process
The cryogenic distillation process is ideal for generating nitrogen and oxygen on a large scale with high purity. It produces nitrogen through liquefaction and separation of atmospheric air into its constituent parts. The desired gas is distilled to the requirements of the industry. The process starts with the inlet of atmospheric air for compression and ends at the storage outlet.
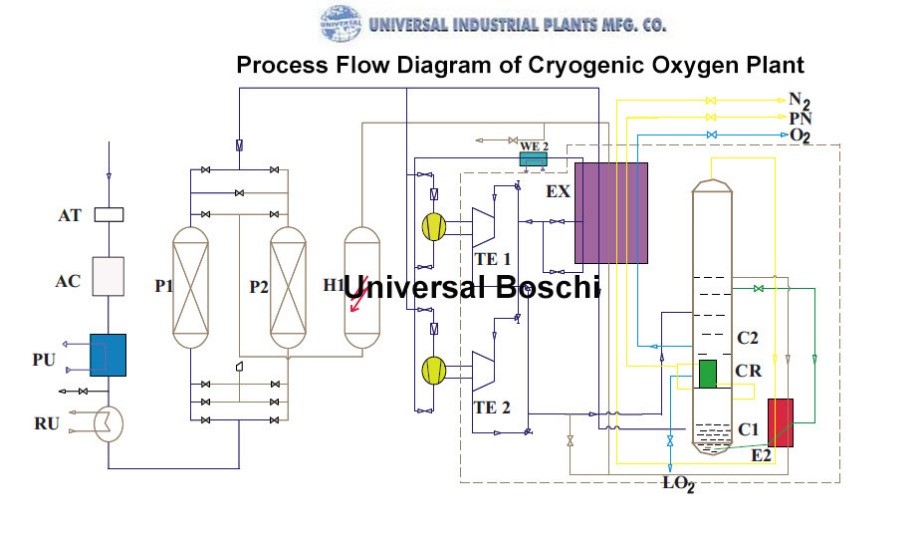
Atmospheric air is taken inside the air separation unit where it is compressed. Then, the air is directed into a cleanup system where impurities such as moisture, hydrocarbons, and carbon dioxide are eliminated. Then, the air is moved into the heat exchangers where it is cooled to extremely low temperatures. Then, the air moves into a high distillation column where physical separation of the air into nitrogen and oxygen takes place. Nitrogen is formed at the top of the column and oxygen at the bottom. The desired gas, in our case nitrogen, is collected and moved into a low-pressure distillation column where it is distilled to meet commercial requirements. Nitrogen is collected from here and is stored in a cryogenic nitrogen tank.
For efficient functioning of the process, the plant or generator machinery must be fabricated with ASME quality materials that can withstand extreme pressures and temperatures. The plants/ generators based on the cryogenic distillation process (oxygen plant manufacturers) are often accompanied by a storage tank, liquid pump, vaporizers, temperature, and pressure control monitors.
Also read about:
9 Things You Can Give to Your Car Lover Friend This Holiday Season
Pros and Cons of Having Multiple Savings Accounts
Custom Jewelry Cardboard Boxes The Most Popular Choice